Как сделать шкив своими руками в домашних условиях?
Шкив является одной из наиболее важных запчастей и для сверлильного, и для токарного станка. Он представляет собой деталь, предназначение которой заключается в регулировке скорости и мощности работы двигателя. Конечно, заводские шкивы обладают высокой степенью надежности и спроектированы под свой станок, к которому идеально подходят.
Но со временем шкив, как и множество других деталей, выходит из строя и требует замены. В этой статье мы расскажем, как сделать шкив своими руками. Качественно сделанная вручную деталь может и не уступать по надежности заводским аналогам.
Общие рекомендации
Существует несколько взглядов на изготовление шкивов для станков в домашних условиях. Большинство споров ведется на тему материала, из которого следует изготавливать эту деталь. Специалисты утверждают, что выполнять шкив из дерева – плохая затея. Дело в том, что во время эксплуатации станка на шкив припадает довольно серьезная термическая и физическая нагрузка. Деревянная деталь в таких условиях проработает не слишком долго.
Лучше всего в тяжелых условиях повседневной работы проявляют себя шкивы, сделанные из металла, но их изготовление требует специального оборудования и высоких навыков токаря. Средней по качеству и сложности создания (по сравнению с металлом и деревом) является самоделка, выполненная из фанеры. Такую деталь можно использовать и при ремонте заводского станка, и в процессе создания собственного аппарата.
Шкив из фанеры в домашних условиях
Шкив для любого станка можно выполнить без привлечения токаря. Для этого рекомендуем взять фанерный лист с толщиной около 10 миллиметров и придерживаться следующих инструкций:
- Размечаем поверхность фанеры в соответствии с планируемыми габаритами нашей детали. Стоит отметить, что эти параметры необходимо учитывать и при выборе листа фанеры.
- Нарезаем круги из нашего материала. Для этого рекомендуем использовать лобзик. В ходе работ особое внимание обратите на качество разрезов и целостность заготовок.
- Учитывая толщину нашей фанеры (1 см) вырезаем из нее 6 кругов.
- Берем три вырезанных круга и с помощью дрели высверливаем в их центре отверстия. Их размеры надо сопоставлять с диаметром вала двигателя нашего станка. Сверлить дырки следует таким образом, чтобы их диаметр был меньше его диаметра на 1-2 миллиметра.
- Соединяем три круга с отверстиями при помощи клея и саморезов, которые сверлим по краям заготовок.
- Отверстие созданной нами детали расширяем при помощи круглого напильника до такой степени, чтобы заготовка плотно садилась на вал двигателя.
- Три фанерных круга без отверстий тоже ставим на клей и соединяем при помощи саморезов. После того как эти круги будут надежно закреплены между собой, мы посредством более длинных шурупов крепим их к основному валу.
- Шесть скрепленных фанерных кругов необходимо обточить. Лучше всего это делать с помощью стамески или напильника. Выполняя эту работу необходимо помнить, что качество обточки напрямую будет влиять на функционирование самодельного шкива.
Стоит отметить, что таким же образом можно делать не только приводной шкив, но фланец для наждачной бумаги и другие типы насадок. Кроме того, в ходе самостоятельного изготовления шкива необходимо учитывать и тип ременной передачи, который будет использоваться на станке. Если передача будет зубчатой, то и шкив следует сделать зубчатым. Формирование такой детали будет занимать намного больше времени, ведь на заготовке придется еще делать и зубья.
Видео: как сделать шкив?
Делаем алюминиевую деталь
Сделать металлический шкив сложнее, чем его фанерный аналог, но и надежность такой детали будет значительно выше. Предоставляем детальную пошаговую инструкцию по изготовлению алюминиевого шкива. Для производства этой детали нам понадобится кусок алюминия и приспособление для его переплавки.
- Заготавливаем форму из пенополистирола. Перед тем как это сделать, определитесь с необходимыми размерами для вашего шкива.
- Выплавляем алюминий. Лучше всего это делать в специальной плавильной печке.
- Расплавленный алюминий выливаем в форму.
- Монтируем планшайбу и выплавленную деталь. Для этого в заготовке необходимо просверлить отверстия и скрепить элементы посредством саморезов.
- Обтачиваем нашу деталь. Это можно сделать с помощью болгарки.
- Делаем в нашем шкиве отверстие дрелью.
Необходимо отметить, что изготовление металлического шкива требует определенных навыков и ресурсов. Для его самостоятельного производства придется потратить намного больше времени и энергии, но такие затраты окупятся длительным сроком эксплуатации такой детали. Перед выплавкой необходимо также убедиться в том, что ваш алюминий обладает достаточной прочностью и пригоден для приготовленной ему функции.
metmastanki.ru
Как сделать шкив без токарного станка
На видео-канале «Э+М» показана технология изготовления шкивов из простых и доступных материалов с использованием доступного инструмента. При этом будем обходиться без токарного станка. Во второй части публикации еще одна технология — другого мастера.
Приступим к изготовлению. Для изготовления 1 типа понадобятся следующие материалы. Суперклей, листовая жесть, линолеум, термоклей и спица велосипеда.
Изготовление начинаем с разметки. Для этого откладываем нужный радиус циркулем и линейкой. Чертим круг на металле. Теперь откладываем ещё один радиус, но на один миллиметр меньше, чем на предыдущих дисках. Чертим окружность на линолеуме. Сверлим отверстие 2 миллиметров под ось. Прикладываем центр диска и линолеума к центру из жести. Переворачиваем с другой стороны делаем отверстия через трафарет.
Ось изготавливается из велосипедной спицы. Чтобы откусить воспользуемся бокорезами или плоскогубцами. Собираем и соединяем детали между собой клеем. Так как вас проворачивается, фиксируем термоклеем. На фото пример, где используется подобный шкив.
Чтобы изготовить 2 типа шкива, нужно два материала. Листовой пвх пластик из плоской вентиляционной трубы ось из велосипедной спицы. Технология почти такая же, как в 1 случае. Здесь также используется токарный станок.
Итак, на видео показано простая технология изготовления шкива с применением обычных инструментов, без обращения к помощи токаря. Здесь не требуются никакие станки.
Еще одна технология работы по созданию шкива без применения токарного или иного станка.
В этом видеоролике канала «Mr.10000Bees» рассказали о технологии создания шкива из фанеры. Этот метод предполагает работа без токарного станка.
Имеется движок от стиральной машинки. Для непрофессиональных работы его мощности хватит.Токарь удлинил вал, сделал симметричным с обеих сторон. Сейчас стоит задача сделать ведущий шкив без привлечения токаря. Диаметр 95 миллиметров. Фанера десятка. Лобзиком выпилить 5 кругов. Диаметр 100 миллиметров. Соединим заготовки клеем, посадим на вал и будем обтачивать. Оказалось, что толщина фанеры 12 миллиметров, поэтому достаточно 5 дисков. Суммарная толщина 60 миллиметров. Так как планируется использование стандартной ленты для шлифмашин, такого круга для ширины ленты достаточно.
В 3 кругах перьевым сверлом сверлить отверстия. Диаметр вала 14 миллиметров, поэтому сверло 12. Складываем вместе. Мажем клеем и фиксируем саморезами. После всех манипуляций получился блин. Его толщина равна толщине, которую хотим насадить на вал.
Диаметр вала почти на 2 миллиметра больше. Необходимо соблюсти соосность, так как внутри всё равно есть перепады. Вставляем внутри круглый напильник. Придерживая руками с двух сторон напильник, прокладываем колесо несколько раз. Как увеличить внутренний диаметр и соблюдем соосность.
После этих процедур берём два оставшихся круга, склеиваем и крепим саморезами. Таким образом можно сделать не только ведущий вал для гриндера, но и флянец для наждачного камня. Либо любой другой насадки на наждак.
Ролик насадили на вал. Обтачивать будем на включенном двигателе. Центрация самого вала тоже не стопроцентная, но это не критично. Если вы хотите делать такой вал, то обязательно можете клеем. Молотком непосредственно на шкив не бейте, только через оправку. Можно использовать кусочек фанеры. Потихоньку, легкими ударами насаживается.
Шкивы из фанеры и прочие способы ремонта станков на коленке
У многих при восстановлении станков из ничего возникают проблемы со шкивами. Я эту проблему решил просто. Выточил их без посторонней помощи из 18 мм. фанеры. Забегая наперед, на таких шкивах обычную сталь можно снимать 0,2 мм. Визжит станок, конечно, если плохо резцы заточены.Останки станка попались практически даром без ЗБ и суппорта. Зато с патроном. ЗБ у меня появилась благодаря Александру (A.N.) с этого форума, за что ему большое спасибо, а суппорт случайно выцепил на барахолке. Как разбирал ПБ, я уже писал в теме «У 1Д601 шпиндель сложно вынуть», как собирал, будет отдельная тема с чертежом в разрезе. Пригодится начинающим. А пока точим шкивы из фанеры.
Малый шкив для точности и убыстрения процесса точил на вот таком чуде. Это извращение на тему Fonly.
Для таких диаметров, это «станок» не предназначен, так что пришлось упор для резцедержателей убрать и точить используя опоры из подходящих по ширине всяких металлических пластин. Для маленького шкива угол ~36 градусов. Ремень нулевой. Подробности не расписываю, так как этот шкив садится на уникальный пластмассовый шкив на двигателе 120 Вт от какой-то советской выжималки и скорее всего последователей у меня не будет. Решение уникальное и временное, пока зима. Нет желания по морозу рыскать за приличным однофазником. В планах все равно переделка.
Гораздо точнее шкив можно выточить прямо на вале двигателя. Выпиливаем две примерно круглых фанерки 18 мм. Одна будет шкивом, другая (поменьше диаметром) используется для закрепления на вале двигателя. Скручиваем их (4-6) винтами. Во второй сверлим 4 отверстия под 90 градусов, нарезаем резьбу, крепим. Если вал срезан или есть паз, то вообще шикарно. Один винт туда и ничего не провернется. На подходящем куске толстого ДСП крепим двигатель и резцедержатель. Работаем через автотрансформатор на 110 вольтах без конденсатора. Подали напряжение на рабочую обмотку, крутанули в нужную сторону, двигатель завертелся. Полюсов в 2 раза меньше т.к. одна обмотка, скорость меньше, мощность меньше, безопасность работ выше. Точим обычным образом. Для дерева достаточно иметь отрезной резец и все. А вот точить большой шкив, как предлагают некоторые, закрепив вал двигателя в кулачки патрона, по-моему, не следует. Во-первых, не факт, что кулачки не со смещением, значит надо двигатель как-то центровать относительно оси шпинделя. А во-вторых, представьте, как двигатель вообще в этом случае крепить на станине? Мой способ реальнее и главное быстрее.
Большой шкив делал с помощью импровизированной сверлики на базе штатива от фотоувеличителя Крокус. Получилась весьма удобная штука просто из хлама.
Процесс описываю подробно, для возможных последователей. Единственно, у меня имеется переходник для дрели к наждачным кругам с диаметром внутреннего отверстия 20 мм. Оказался очень удобен для моих целей.
Малый шкив тоже протачивался на нем. Нужно иметь похожую железяку с минимальным биением и диаметром не более 21 мм, т.к. придется еще растачивать отверстие шкива до диаметра 22 мм. Кроме того, у него должен быть резьбовой выступ, который будет опирается на кусок фанеры.
Разметил и вырезал подобие круга из фанеры. Сверлом Фостера засверлил в заготовке отверстие Ф20. Сделал шаблон в виде трапеции с углом на 34 градуса, для периодической проверки шкива. В шаблоне должно быть учтено, что в шкиве проточка глубже, чем высота ремня на 1,5 мм., который будет растягиваться и немного съедаться в процессе использования. Размеры профиля канавки искал по фразе размеры «шкивы для приводных клиновых ремней». Там и табличка дается всех размеров для разных ремней.
Чтобы нормально передавать усилие через этот шкив(для надежности, все-таки дерево), нужна еще стальная шайба с внутренним отверстием 22 мм и пазом для штифта. Шайба из магазина стройматериалов (40 мм в диаметре).
Высверливаем в шайбе тонкими сверлами по контуру отверстие такого диаметра чтобы его можно было довести круглым напильником и надфилем до 20 мм. Не торопимся, нужно чтобы без большого зазора в этом отверстии вращалось сверло Фостера. Чисто слесарная работа.
В шайбе делаем два технологических отверстия для гвоздей и прибиваем ее гвоздями к центру заготовки шкива. Насквозь в шайбе и заготовке сверлим 6 отверстий 3,2 мм. и насквозь же нарезаем резьбу М4.
Делаем в центре заготовки отверстие для кончика сверла Фостера с запасом, опускаем сверло до дерева и на малых оборотах аккуратненько просверливаем заготовку. Если имеется только многозубая фреза подходящего диаметра, придется сверлить без шайбы, чрез намеченный в фанере центр. Будет менее точно, но для наших целей терпимо.
Отверстие Ф22 в шайбе растачивал на подобии токарника, г-образным резцом проточив сначала оправку для деревянного круга. Потом в круге проточил место по внешнему диаметру для установки шайбы. Аккуратненько прибил мелкими гвоздиками и ручной дрелью наметил центра для отверстий в деревяшке. Потом сверлом 3.2 просверлил и нарезал резьбу. Резьбу резал через резьбу в отверстиях шайбы, чтобы совпала. Потом закрепил и проточил немного на плюс Ф22. Точил через прокладки 0,1 мм. Извращение, конечно, но я привычный.
Можно это сделать и вручную, разметив отверстие 22 мм штангель-циркулем и аккуратно обработав внутреннюю часть круглым напильником.
Насадил заготовку на переходник, закрепил в патроне сверлилки и вперед. Сначала обточил грубым напильником для металла, чтобы максимально было похоже на круг. От пыли, включил пылесос. Потом разметил поверхность заготовки по ширине, чтобы ножовкой прорезать три паза на глубину 6,5-7 мм. Расстояние между пропилами около 2,0 мм. С учетом ширины пропила(полотна ножовки), после всех операций должен появиться прямоугольный паз шириной около 6 мм. Хотя нижняя часть моего ремня по ширине ~7 мм., нужен запас устранения возможных ошибок.
Для дальнейшего удобно испортить какую-нибудь лишнюю стамеску и по шаблону сделать специальный трапециидальный фасонный резец. У меня ее не оказалось, и пришлось все делать длинным отрезным резцом с широкой(3 мм) режущей частью. Сначала выбирал полоски фанеры между пропилами, потом использовал резцедержатель от выше приведенного подобия «токарного» станка. Только точить нужно боком, использую прокладки, чтобы одно относительно другого перемещать. Выставлял его по транспортиру на нужный угол (примерно по 17 градусов в ту и другую сторону) ставил боком и протачивал паз с каждой стороны, проверяя по шаблону. Повторяю, фасонным резцом все это делается гораздо проще.
В конечном счете получился паз примерно до 8,5 мм.
Теперь о технике безопасности. Дрель у меня с регулятором оборотов. Работать нужно на низких оборотах, резец должен быть практически перпендикулярен обрабатываемой поверхности. Иначе будет сильно вгрызаться в дерево и его выбивает из рук. И желательно прибивать к фанере какие-нибудь упоры для удобства.
В любом случае при такой технологии изготовления шкив будет немного бить, но это не страшно. Совсем не обязательно для работы с фенерой очень сильно натягивать ремень. Проверено не проскальзывает.
Этот шкив нужен только для того, чтобы уже на работающем станке выточить нормальный. Такой вот промежуточный этап для тех, у кого нет возможности заказать сразу алюминиевые шкивы нормальному токарю. Я детали для сборки шпинделя ждал месяца два, и то, что обошлись они мне не дорого, как-то не радовало. Так что, потерянный вечер на промежуточный шкив в сравнении с этим ничто, а результат на лицо.
Вот фото результата.
Для проточки более-менее нормального большого шкива я использовал вот такой бутерброд(собран для наглядности из старого шкива):
Мне повезло. Была подходящая железка, из которой получилась импровизированная «планшайба». Такой удобной железки под руками может и не быть, поэтому в конце дам совет как без нее обойтись.
В ней было высверлено 6 отверстий 2,5 мм. Масимально по центру к ней двумя струбцинами крепится шайба из строймагазина, а лучше специально обрезанная по размеру, скругленная по контуру, не гнутая пластина из 3 мм. стали (шайбы часто немного неровные), в которой насквозь сверлятся 6 отверстий. Шаблон «планшайба». Дальше вырезается из хорошей 18 мм. фанеры подобие круга нужного диаметра, и проделываются отверстия и в нем. Шаблон шайба, в которой сверлится 2 технологических тонких отверстия для гвоздиков, через которые она прибивается к фанере перед сверлением. Затем гвозди убираются, весь этот «бутерброд» скрепляется и все отверстия засверливаются насквозь сверлом 3,2 мм. Для центровки частей перед скреплением использовал несколько концевиков от сломанных свёрел 2,5 мм. чтобы в процессе скрепления и сверления ничто не смещалось. Я никогда не выкидываю остатки сломанных сверел. При таких работах они бывают не заменимы, так как целые сверла слишком длинные и часто мешают сверлить(упираются в патрон). Под конец использовал уже хвостовики от сломанных свёрел на 3,2 мм. чтобы части бутерброда не сместились относительно друг друга. В заключении машинным метчиком насквозь нарезается резьба М4.
Далее скрепляем полученные детали следующим образом. Тремя винтами к «планшайбе» прикручиваем шайбу, Длина винтов должна быть такой, чтобы не они не выходили за поверхность шайбы. Заготовку шкива прикручиваем с другой стороны насквозь, через шайбу и «планшайбу». Все это зажимаем в патрон и вуаля! Пару резцов и новый шкив будет очень быстро готов. Не забудьте использовать пылесос для сбора деревянной пыли во время работы. Иначе надышитесь ею.
При подготовке шайбы исходите из наличия резцов. Проще, как и писал ранее, высверлить мешающий метал. Тогда меньше обрабатывать. А внутреннюю часть довести до ума боковой гранью отрезного резца заточенного так, чтобы ничего не мешало им пройти 3 мм. Если резцы имеются, то можно делать правильно по книжкам для токарей. Для такой работы я резцы из твердосплава подтачивал мелким алмазным надфилем.
Сначала делаем отверстие Ф22 с минимальным плюсом в шкиве. Я окончательно промерял отверстие подшипником с внешним диаметром 22 мм. Удобнее чем штангелем лазить. Потом шкив снимается и растачивается Ф22 в шайбе. Скрепляем шайбу и шкив в месте шестью винтами, приличная соосность после сборки гарантирована. Главное найти соответствующие отверстия. Я при первичной сборке (до сверления «бутерброда») метил заготовки делая риски напротив друг друга. Делаем сквозной паз и насаживаем на конец шпинднля. Чтобы дерево не сминалось при затяжке гайки на вторую сторону нужно изготовить кусок стали 1 мм. с отверстием Ф22.
И вот результат, правда, пока полуфабрикат:
И как обещал, про «планшайбу». Ищем цилиндрический кусок дюраля(легче обрабатывать чем сталь) мм 25-30, в патрон его и торцуем хоть отрезным резцом. Суперповерхность не нужна. Потом вырезаем из куска ровной пластины Д16(Т) миллиметров 6-8 подходящий кусок примерно круглого сечения, хотя это не обязательно. Хоть квадрат, потом можно обточить на станке, сверлим в нем примерно по центру три отверстия 3,2 мм. под 120 градусов, с расчетом, что потом через них будем сверлить отверстия в торце кругляка для закрепления. Центры отверстий не должны быть ближе 6 мм к боковой поверхности кругляка. В кругляке нарезаем резьбу М4, а в пластине сверлим Ф4 и зенкуем с расчетом утопить на 1 мм винты «впотай». Зажимаем собранную деталь в патрон и протачиваем поверхность, чтобы не било. Острым концом резца намечаем круг, по которому будем сверлить 6 отверстий, а дальше как было описано. Если сомневаетесь в прочности такой «планшайбы» используйте винты М5 или сталь.
Надеюсь ничего не упустил.
www.chipmaker.ru
Изготовление шкива
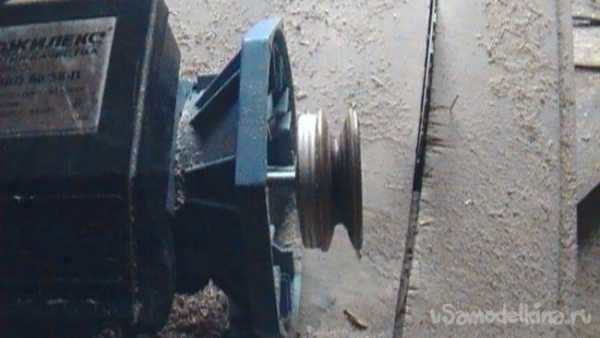
Иногда может потребоваться шкив определённого размера, но где его взять? Предлагаю способ изготовления шкива непосредственно на валу электродвигателя.
Для изготовления шкива мне потребовалось: фанера – 10 мм.; клей; пила циркулярная; крупный напильник; ножовка по металлу; наждачная бумага и сам электродвигатель. Двигатель я взял от насосной станции, насос вышел из строя, а ремонтировать нет необходимости.
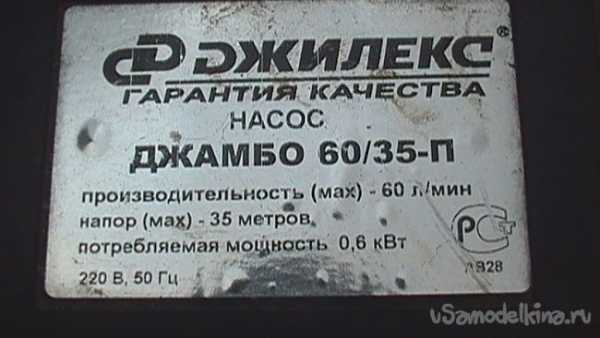
Из — за того, что вал двигателя изготовлен немного под конус, я изначально поставил стальную шайбу для исключения проскальзывания фанеры дальше по валу. Далее поставил кусок фанеры и через вторую шайбу подтянул её гайкой. С помощью циркулярной пилы сделал круг и убрал биение.

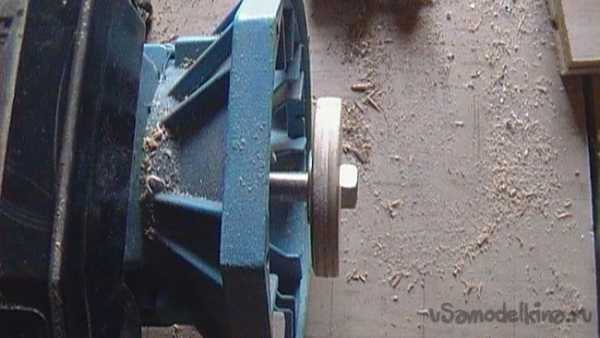
Думаю, что он мне послужит.
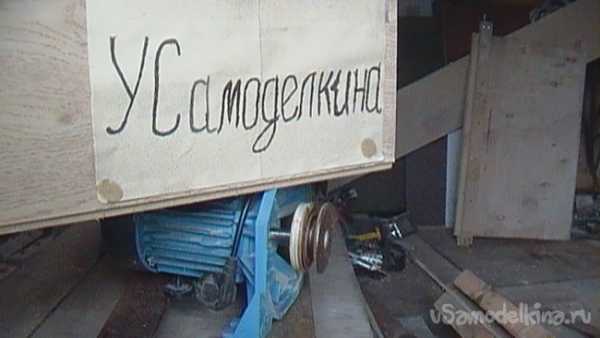
Напоследок видео:
Всем удачи в делах! Становитесь автором сайта, публикуйте собственные статьи, описания самоделок с оплатой за текст. Подробнее здесь.
usamodelkina.ru